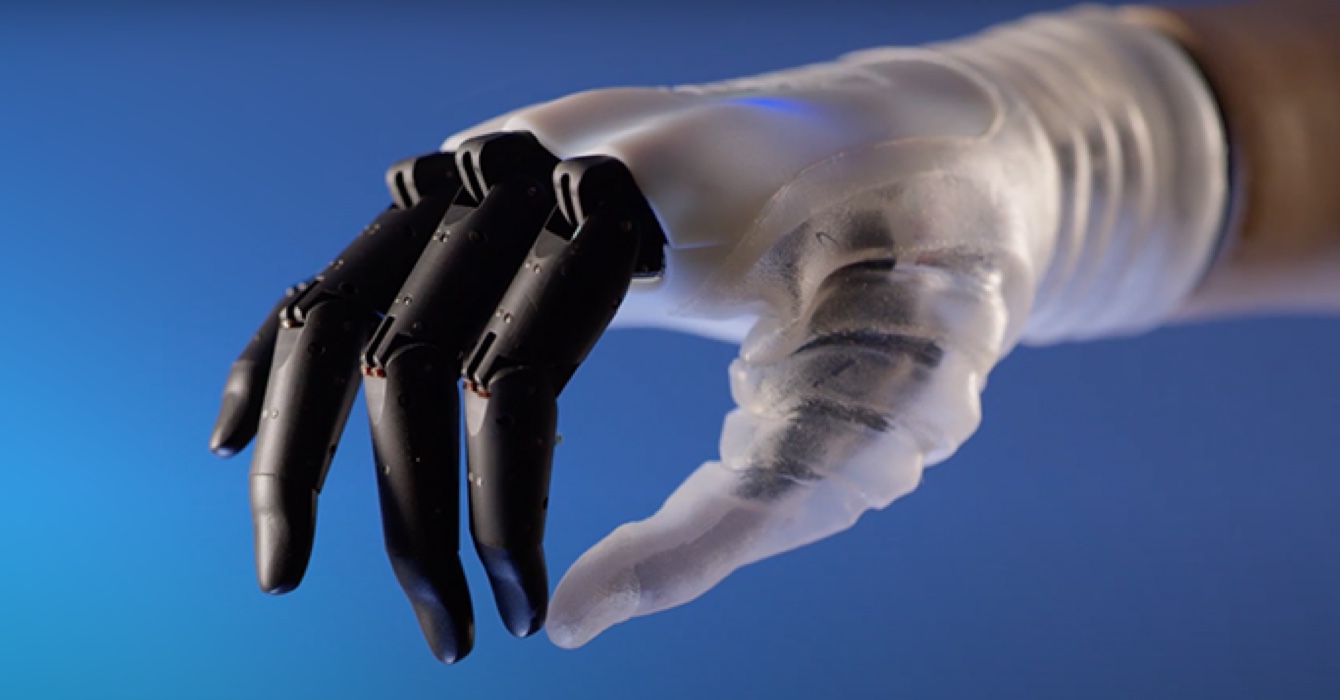
A Significant Contribution to the Hannes Project
MICROingranaggi designed and manufactured the gear motor at the heart of Hannes, the robotic-derived prosthetic hand developed by the Italian Institute of Technology in collaboration with Inail. This is an innovative project not only technologically but also conceptually.
A Precise Technological Choice
A robotic-derived prosthetic hand that allows patients to reproduce most of the functionalities of a natural hand. Cost: between 5,000 and 10,000 euros, which is about 40% less than devices currently on the market with similar functions. We’re talking about Hannes, the prosthetic hand developed in 2018 by the Rehab Technologies Lab, the joint lab created through the collaboration between Inail and the Italian Institute of Technology (IIT). The name "Hannes" is a tribute to Professor Hannes Schmidl, former Technical Director of the Inail Prosthetics Center in Vigorso di Budrio (Bologna). Hannes is controlled by the contraction of the residual muscle of the missing limb using surface sensors that capture the electrical signal from the brain. After being cleaned and amplified, the signal is transmitted to a motor controller board, which directs the motor responsible for moving the fingers. The technological choices underlying the development of this prosthetic hand start from a specific concept: designing very complex prosthetics can result in devices that are difficult to use and have significant limitations. Hannes, on the other hand, is easy to use and control.
Samuel Stedman, a mechanical and robotics engineer at the Italian Institute of Technology, answers some questions about the project and the collaboration with MICROingranaggi.
How and when did the idea to create the "Hannes" project come about?
“Each year, INAIL spent millions of euros on purchasing prosthetic hands from foreign manufacturers and started to consider developing one internally in Italy. Thus, five years ago, the Hannes project was launched to develop a prosthetic hand based on an underactuated system, a type of mechanism that has only one motor but five or six degrees of freedom (commonly known as DOF). The choice to base the project on this type of system made Hannes function very differently from most prosthetics on the market. Thanks to a kind of "intelligence" built into the product itself, it could automatically adapt very naturally to the object being grasped, regardless of its intrinsic characteristics (hard, soft, large, small). All this without the need for overly sophisticated control.”
So, how exactly does Hannes work? What are the advantages compared to similar projects realized so far?
“Hannes is a myoelectric hand. Two EMG (electromyography) sensors are placed on the stump of the amputated arm in a specific position relative to the severed muscles. When the patient tries to move the hand that no longer exists, electrical impulses from their brain are intercepted and read by these EMG sensors, then amplified to be sent to another board within the hand. Here, the signal is cleaned, filtered, and sent to a motor controller board (the so-called interpreter) in the prosthetic hand, which instructs the motor to move, allowing the hand to open and close. Attached to the hand’s motor is a gear motor developed by MICROingranaggi, located in the central part, which, through a special pulley, controls a series of cables that pass through all the fingers, allowing the hand to move in a precise and articulated way, adapting automatically to the object being grasped. The underactuated system we developed, combined with the gear motor designed by MICROingranaggi, allows for a very natural grip that's easy to control.”
So, more control by the patient and also easier to learn to use it... “Exactly. Designing very complex prosthetic hands can lead to patients struggling to learn how to use them, which greatly limits their use, as it's less cumbersome and more immediate to rely on the other hand for most tasks. The prosthetic hands offered by our competitors usually have a motor for each finger, which allows them to move individually (almost like a normal hand), but at the same time, this makes controlling so many degrees of freedom without external applications complex. Typically, each time the patient wants to change the type of grip, they need to take out their smartphone, enter the specific app, select the desired grip type, initiate it, and then use the hand. This sequence of operations is somewhat unnatural, leading the patient to prefer always using the same function, relying on the other hand for tasks the prosthesis can't perform. We decided to go in the opposite direction, developing a prosthetic hand that had 95% of the functionalities of other similar products on the market, but was easier to control and had one-tenth of the cost (between 5,000 and 10,000 euros compared to 35,000 to 45,000 euros). The choice to integrate only two EMG sensors (open hand, closed hand) and a single motor allows us to significantly reduce the final price while also simplifying control and usage.”
The gear motor at the heart of the hand was developed by MICROingranaggi. Why choose this technological partner? “When we started the project, we had developed an internal gear motor, but it had several issues related to excessive noise and low stability. We decided to seek an external company with extensive experience and expertise in this field, and the choice fell on MICROingranaggi, one of the most well-known companies in Italy in this sector. During the first meeting, we explained the project to MICROingranaggi, detailing what we needed: a gear motor with compact weight and size, low noise, high cable force, low vibration levels, and specific operational friction. This was because less friction (in terms of energy loss during operation) would allow for a less powerful motor, leading to longer battery life with the same usage. Thanks to MICROingranaggi's gear motor, the Hannes hand can now exert a gripping force up to five times higher than other prosthetic hands on the market.”
And was MICROingranaggi able to meet your needs? “Absolutely. MICROingranaggi provided us with a solution consisting of a gear motor and pulley system ready for installation within the hand in just a few steps.”